2025/02/19(水)HB8H 試作1版を製造
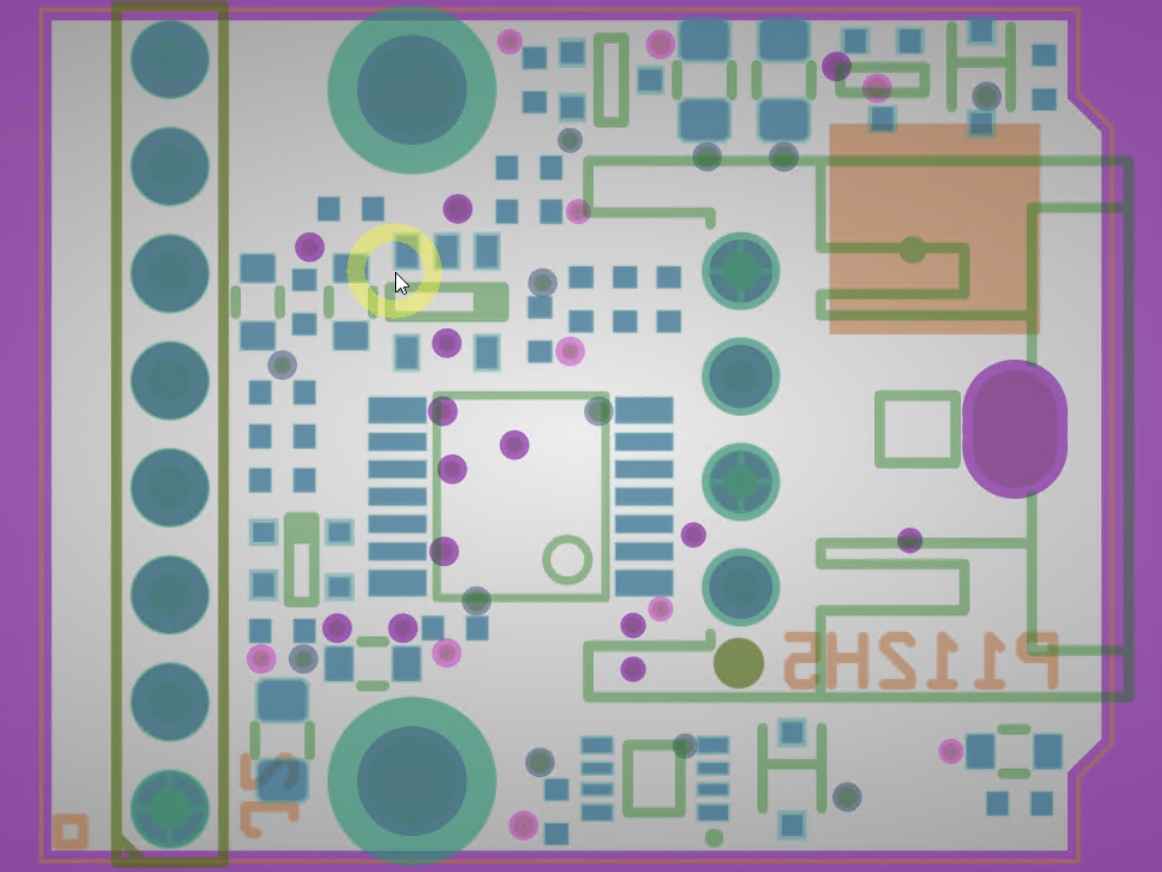
基板生産量
5枚基板刻印
P112H5仮試作版からの変更点
- HAT I/Oコネクタの根元付近にあるチップ部品がケースと干渉する問題を修正
- コネクタを標準タイプからライトアングルタイプに変えた
- 面積削減のため電源監視ICをエイブリック製に変更
- SOT25→SC-82AB
- 面積削減のためダイオードをローム製に変更
- SOT23→SOT323
- 基板サイズを大きくしてケースとの隙間を埋めた
- 幅(mm, 最大): 24.6→25.4
シリアルコード
3502025/02/07(金)HB8H 仮試作品の回路基板
2025/01/28(火)Application Note QFN and SON PCB Attachment
https://www.ti.com/lit/an/slua271c/slua271c.pdf
www.ti.com Table of Contents Application Note QFN and SON PCB Attachment Steve Kummerl, Bernhard Lange, Dominic Nguyen Texas Instruments ABSTRACT Quad flatpack no lead (QFN) packages and small-outline no lead (SON) packages are leadless packages with electrical connections made through lands on the bottom side of the component to the surface of the connecting substrate (PCB or ceramic). This application report includes introductory information about attaching QFN and SON devices to printed circuit boards (PCBs). Table of Contents 1 Texas Instruments Quad Flatpack No Leads and Small-Outline No Leads.......................................................................3 1.1 Introduction........................................................................................................................................................................ 3 2 Manufacturing Considerations..............................................................................................................................................4 2.1 SMT Process......................................................................................................................................................................4 3 Printed Circuit Board (PCB) Design Guidelines.................................................................................................................. 5 3.1 Land Pad Styles................................................................................................................................................................. 5 3.2 Land Pad Design................................................................................................................................................................5 3.3 Lead Finger Pad PCB Design............................................................................................................................................ 6 3.4 Exposed Pad PCB Design................................................................................................................................................. 7 3.5 Solder Mask....................................................................................................................................................................... 8 3.6 Surface Finishes................................................................................................................................................................ 9 3.7 Board Layout Considerations.............................................................................................................................................9 4 Solder Paste Screen Printing Process............................................................................................................................... 10 4.1 Solder Paste.....................................................................................................................................................................10 4.2 Solder Stencils................................................................................................................................................................. 10 4.3 Lead Finger Stencil Design.............................................................................................................................................. 10 4.4 Exposed-Pad Stencil Design............................................................................................................................................ 11 5 Package to Board Assembly Process................................................................................................................................ 13 5.1 Placement and Alignment................................................................................................................................................ 13 5.2 Solder Reflow...................................................................................................................................................................13 SLUA271C 窶� JUNE 2002 窶� REVISED DECEMBER 2023 Submit Document Feedback Copyright ツゥ 2023 Texas Instruments Incorporated QFN and SON PCB Attachment 1 Trademarks www.ti.com 5.3 PCB Cleaning...................................................................................................................................................................14 5.4 Inspection.........................................................................................................................................................................14 6 Rework Guidelines (Hot Gas Convection and Manual).....................................................................................................16 6.1 Compound Removal........................................................................................................................................................ 16 6.2 Site Redress.....................................................................................................................................................................17 6.3 Component Replacement and Reflow............................................................................................................................. 17 6.4 Manual Rework Considerations....................................................................................................................................... 19 7 Revision History................................................................................................................................................................... 20 List of Figures Figure 1-1. QFN Structure........................................................................................................................................................... 3 Figure 2-1. Packing Material Label Information With Moisture Sensitivity Level (MSL).............................................................. 4 Figure 3-1. QFN and SON Outline Dimensions...........................................................................................................................5 Figure 3-2. PCB Land Pattern..................................................................................................................................................... 6 Figure 3-3. Substrate or PCB Lead Finger Geometry................................................................................................................. 6 Figure 3-4. X-Ray Images for Reference.....................................................................................................................................8 Figure 3-5. PCB Solder Mask and Keep-Out Area Example....................................................................................................... 8 Figure 3-6. Avoid Excessive Bending.......................................................................................................................................... 9 Figure 4-1. Solder Stencil Profile............................................................................................................................................... 10 Figure 4-2. Aspect and Area Ratio Illustration........................................................................................................................... 11 Figure 4-3. Example Land Pattern and Exposed-Pad Stencil Design....................................................................................... 12 Figure 5-1. Package Self Alignment at Reflow.......................................................................................................................... 14 Figure 5-2. QFN and SON Pb and Pb-Free Example Reflow Profiles.......................................................................................14 Figure 5-3. Illustration of Typical Fillet Formation...................................................................................................................... 15 Figure 6-1. Example Mini Stencil............................................................................................................................................... 18 Figure 6-2. Example Hot Gas Convection Nozzle..................................................................................................................... 18 Figure 6-3. Preheater.................................................................................................................................................................19 Figure 6-4. Manual Rework Damage.........................................................................................................................................20 List of Tables Table 2-1. Essentials for Assembly Quality..................................................................................................................................4 Table 3-1. PCB Dimension Definitions.........................................................................................................................................6 Table 6-1. Pb-Free Solder Component Removal.......................................................................................................................16 Table 6-2. Pb-Free Solder Component Placement.................................................................................................................... 19 Trademarks All trademarks are the property of their respective owners. 2 QFN and SON PCB Attachment SLUA271C 窶� JUNE 2002 窶� REVISED DECEMBER 2023 Submit Document Feedback Copyright ツゥ 2023 Texas Instruments Incorporated www.ti.com Texas Instruments Quad Flatpack No Leads and Small-Outline No Leads 1 Texas Instruments Quad Flatpack No Leads and Small-Outline No Leads 1.1 Introduction Quad flatpack no lead (QFN) packages and small-outline no lead (SON) packages are thermally enhanced plastic packages that use conventional copper leadframe technology. This construction results in a cost-effective advanced packaging solution that helps to maximize board space with improved electrical and thermal performance over traditional leaded packages. QFNs have solder lands on all four sides of the package. SONs typically have solder lands on two sides of the package. QFNs and SONs are available in a number of formats. QFNs and SONs are molded and mechanically singulated from a matrix leadframe. Package size is determined by several key factors including die size, number of terminations, etc. All QFNs and SONs are leadless packages with electrical connections made via lands on the bottom side of the component to the surface of the connecting substrate [printed circuit boards (PCB), ceramic]. The standard QFN and SON package has an exposed pad that enhances the thermal and electrical characteristics, enabling high-power and high-frequency applications. Note This QFN and SON PCB application report is intended as a guide. Precise process development and experimentation are needed to optimize specific applications/performance. QFN STRUCTURE AND STITCH BONDS Figure 1-1. QFN Structure SLUA271C 窶� JUNE 2002 窶� REVISED DECEMBER 2023 Submit Document Feedback Copyright ツゥ 2023 Texas Instruments Incorporated QFN and SON PCB Attachment 3 Manufacturing Considerations www.ti.com 2 Manufacturing Considerations 2.1 SMT Process Many factors contribute to a high-yielding assembly process. A few of the key focus areas and their contributing factors are highlighted in Table 2-1. Table 2-1. Essentials for Assembly Quality Solder paste quality Uniform viscosity and texture. Free from foreign material. Solder paste must be used before the expiration date. Shipment and storage temperatures must be maintained at the proper temperature. Paste must be protected from drying out on the solder stencil. PCB quality Clean, flat, plated, or coated solder land area. Attachment surface must be clean and free of solder-mask residue. Placement accuracy Tight tolerances are not usually required. QFN and SON packages self center as long as a major portion (more than 50%) of the lead finger is in contact with the solder-paste-covered land area on the board. Alignment marks (fiducials) on the PCB are helpful for verifying correct placement of parts. Solder reflow profile The solder reflow temperature is dependent on the PCB design, PCB thickness, and peak reflow temperature according to the moisture sensitivity level (MSL) of components, component density, and the recommended profile of the solder paste being used. A reflow profile must be developed for each PCB type using various QFN and SON packages. See Figure 5-2 in Section 5.2 for the reflow profile. Solder volume Solder volume is important to ensure optimum contact of all intended solder connections. Ordered PN Customer E4 Inner Box/Reel Labels MSL Caution Label JEDEC Pb-Free Logo & Finish Code High-Temp & Low-Temp MSL Ratings Assembly Site & Assembly Date Code (YYWW) Figure 2-1. Packing Material Label Information With Moisture Sensitivity Level (MSL) 4 QFN and SON PCB Attachment SLUA271C 窶� JUNE 2002 窶� REVISED DECEMBER 2023 Submit Document Feedback Copyright ツゥ 2023 Texas Instruments Incorporated www.ti.com Printed Circuit Board (PCB) Design Guidelines 3 Printed Circuit Board (PCB) Design Guidelines One of the key efforts in implementing the QFN and SON package on a substrate motherboard is the design of the land pad. The QFN and SON has lead fingers exposed on the bottom side of the package. Electrical and mechanical connections between the component and motherboard can be made by soldering the part using screen printed solder paste and reflowing after placement. To ensure consistent solder joint geometries, it is essential to design the land pattern considering the component exposed leadframe pattern. 3.1 Land Pad Styles There are two basic designs for PCB land pads for the QFN and SON package窶杯he copper defined or nonsolder mask defined style (NSMD) and the solder mask defined style (SMD). The industry has debated the merits of both styles of land pads and although TI recommends the copper defined style land pad (NSMD), both styles are acceptable for use with the QFN and SON package. NSMD pads are recommended over SMD pads due to the tighter tolerance on copper etching compared to solder masking. In addition, the NSMD pads help to contain the solder paste within the solder mask opening. NSDM, by definition, also provides a larger copper pad area and allows the solder to anchor to the edges of the copper pads, thus providing an increase in wettable surface area. 3.2 Land Pad Design IPC-7351 is one of the industry standard guidelines for developing PCB pad patterns. Because the QFN and SON is a new package style, this application report is intended as a guide and should be used with the IPC-7351 in designing an optimum PCB land pattern. Figure 3-1 identifies the various QFN and SON dimensions required to design a matching substrate pad pattern. Because most packages are square with dimension D = E and the leads are along the E direction for dual packages, the side-view dimensions (D, S, D2 and L) are used to determine the land length on the motherboard PCB or substrate. Figure 3-2 shows the motherboard PCB or substrate land pattern dimensions to be established. Table 3-1 offers a description of these dimensions. D D D2 D2/2 D/2 INDEX AREA DETAIL B -8- L (D/2 xE/2) E2/2 (NE-1)x e 6 -A- 000 G 2x E S E2 E/2 4 EXPOSED PAD 9 5 N N-1 qqq C 2x (ND-1)x e DETAIL 1 6 DATUM A OR B L e/2 e EVEN TERMINAL SIDE Terminal Tip 5 e Terminal Tip 3 ODD TERMINAL SIDE Figure 3-1. QFN and SON Outline Dimensions SLUA271C 窶� JUNE 2002 窶� REVISED DECEMBER 2023 Submit Document Feedback Copyright ツゥ 2023 Texas Instruments Incorporated QFN and SON PCB Attachment 5 Printed Circuit Board (PCB) Design Guidelines www.ti.com CLL Amax Zmax D2th Gmin Y CPL X Figure 3-2. PCB Land Pattern Table 3-1. PCB Dimension Definitions Symbol Description Amax Outer extents of pad widths per each side Zmax (1) Outside pad terminal dimension typically 0.8 mm larger than the package body as a starting point Gmin (1) Inside pad terminal dimension X Lead pad width Y Lead pad height CLL Corner pad edge to adjacent inside pad distance CPL Central pad to inside edge of lead pad distance which should not be reduced to smaller than 0.2 mm (1) The dimensions Zmax and Gmin are the outside and inside pad terminal dimensions, respectively. X and Y identify the pad width and length, respectively. Clearance dimensions CLL and CPL are defined to prevent solder bridging. 3.3 Lead Finger Pad PCB Design It is recommended that the PCB lead finger pad be designed a minimum of 0,1 mm longer than the package land length (also known as the toe length) and be extended 0,05 mm towards the center line of the package (also known as the heel). TI uses a typical value of 0,4 mm toe length beyond the package body as a standard to optimize solder volume which should be considered as a model starting point for board designs. The PCB pad width must be a minimum 0,05 mm (0,025 mm per side) wider than the terminal width on the package (see Figure 3-3). However, to avoid solder bridging for components having lead pitches of 0,5 mm, the pad width should be reduced to 0,28 mm or smaller. The 0,28 mm width was based on a 0,5 mm pitch component having a max terminal width of 0,3 mm per the mechanical drawing. In the event that a board supplier can't achieve a solder mask web between 0,28 mm wide pads, the width should be reduced to accommodate the board supplier's solder-mask web tolerances. For board designs that require the minimum land pattern, the stencil design parameters of aspect ratio and area ratio must be considered to have a manufacturable land pattern design. Stencils typically are designed with a relationship to the land pattern, so both must be considered closely when minimizing. IPC-7525 describes the necessary parameters when designing the stencil. 0.05 mm 0.4 mm Min 0.025 mm Per Side for Lead Pitches Greater than 0,.65 mm Figure 3-3. Substrate or PCB Lead Finger Geometry 6 QFN and SON PCB Attachment SLUA271C 窶� JUNE 2002 窶� REVISED DECEMBER 2023 Submit Document Feedback Copyright ツゥ 2023 Texas Instruments Incorporated www.ti.com Printed Circuit Board (PCB) Design Guidelines 3.4 Exposed Pad PCB Design The construction of the exposed pad enables enhanced thermal and electrical characteristics. To take full advantage of this feature, the pad must be physically connected to the PCB substrate with solder. The published data for thermal performance, ホクJA, is based on a four-layer PCB incorporating vias that act as the thermal path to the layers, also known as a JEDEC High K board design per JESD51-7. The dimensions of the thermal pad on the PCB should be equal to the exposed pad on the QFN and SON. Adequate clearance (CPL) is necessary to prevent solder bridging. Experiments have concluded that a minimum clearance of 0,2 mm is satisfactory for most designs. 3.4.1 Thermal Pad Via Design The number of vias represented in TI example land patterns located near the end of the data sheets should be considered as an example starting point. Not all applications require vias. The need for vias depends on the amount of power the device dissipates. If the board routing becomes too challenging to employ the use of thermal vias, contact your local TI representative for further guidance. The center thermal pad, however, should always be soldered to the board for mechanical strength and reliability. For thermally challenging applications, TI recommends that the thermal vias be placed on a pitch of approximately 1,0 mm. Per standard PCB manufacturing capabilities, 0,3 mm diameter drill holes are recommended as a starting point, but a smaller via offers less risk of solder volume loss. On applications where solder volume loss through the vias is of concern, plugging or tenting can be used to achieve a repeatable process. Vias that are plugged eliminate the risk of solder volume loss. If plugging the via is not economically suitable, tenting also can offer benefit. Tenting from the back or topside of the board can cause processing issues with some printed circuit board manufacturers due to chemistry entrapment during the plating process. In the case of plugging or tenting from the backside of the board, the voiding potential can increase due to the air trapped within the tented via. Check with your board fabrication site for recommendations. Another solder-mask tenting technique is to tent from the top of the board. The via solder-mask diameter must be 0,1 mm larger than the via hole diameter when tenting. Another variation is to create a cross-hatch pattern of solder mask to create a predictable area of coverage. Trials have shown that via tenting from the top is less likely to produce random voids between the exposed pad and the PCB pad. See Figure 3-4 for x-ray results of various via tenting structures. For finishes that use an organic solder preserve (OSP), not tenting any vias from the top or bottom of board has shown repeatable performance in soldering. In addition, optimizing the profile to achieve maximum flux activity during the critical reflow stage reduces the amount of voiding seen. Trials have shown that an excessive soak time, which activates the majority of the flux before the melting temperature of the alloy, results in large voids. Check with your solder paste manufacturer if an alternative profile can offer more flux activity through the critical melting phase of the alloy used. SLUA271C 窶� JUNE 2002 窶� REVISED DECEMBER 2023 Submit Document Feedback Copyright ツゥ 2023 Texas Instruments Incorporated QFN and SON PCB Attachment 7 Printed Circuit Board (PCB) Design Guidelines www.ti.com ENIG w/Solder Mask Plug OSP No Tenting w/o plating over via OSP Cross Hatch Solder Mask Pattern ツキ OSP = Organic Solder Preserve HASL No Tenting ENIG w/o vias Figure 3-4. X-Ray Images for Reference 3.5 Solder Mask As described in Section 3.1, a non-solder mask defined pad (NSMD) is recommended over solder mask defined (SMD) to produce consistent solder joint geometries. The solder mask can be designed around each individual lead finger for lead pitches 0,65 mm and above. Check with your board fabrication site for solder-mask openings, but typically the NSMD openings are 0,1 mm to 0,14 mm larger than the lead finger pad size. For a lead pitch of 0,5 mm, it is recommended to design the solder mask around all pads on each side with a clearance of 0,05 mm or smaller, so consult your board fabrication site for tolerance requirements. To maximize the solder mask in the corner regions, it is necessary to round the inner corner on each row (see Figure 3-5). This ensures sufficient solder mask in the corner of the PCB footprint design and also prevents the metal feature from encroaching beyond an air gap of 0,2 mm. In addition, it has been observed that some QFN configurations utilize an exposed metal pin 1 feature beneath the component, which has a potential of shorting to a via if present in this region. Therefore, TI recommends maintaining a routing and via keep-out area next to pin 1 on all QFN designs to guard against this risk and offer more flexibility when selecting different suppliers (see Figure 3-5). Figure 3-5. PCB Solder Mask and Keep-Out Area Example 8 QFN and SON PCB Attachment SLUA271C 窶� JUNE 2002 窶� REVISED DECEMBER 2023 Submit Document Feedback Copyright ツゥ 2023 Texas Instruments Incorporated www.ti.com Printed Circuit Board (PCB) Design Guidelines 3.6 Surface Finishes There are a variety of surface finishes commonly available. The key factor in selecting an acceptable surface finish is to ensure that the land pads have a uniform coating. Irregular surface plating, uneven solder paste thickness, and crowning of the solder plating can reduce overall surface mount yields. Bare copper with an organic solderability preservative (OSP) coating, electroless nickel immersion gold, or electroplated nickel-gold finishes have been shown to provide an acceptable land pad surface. One type of surface finish that has shown irregular processing is referred to as a "dry film process". This is because the copper undercut effect caused during the dry film removal prevents optimal sidewall wetting during the reflow process. The advantages of plating over OSPs are: 窶「 Shelf life 窶「 Permanent coverage of copper vias and other features not exposed to a solder process, and 窶「 Contamination resistance Even with these differences, OSPs have shown robust performance in industry. In summary, a controlled assembly process for QFN and SON soldering relies on a flat uniform attachment site. Achieving a flat uniform surface leads to a greater control of solder-paste print uniformity, resulting in an overall robust process. 3.7 Board Layout Considerations There are a wide variety of QFN packages on the market that have varying thicknesses. Location of the thinner format QFN packages should be carefully considered when laying out the board design to avoid regions of extreme deflection during manufacture (see Figure 3-6). Excessive bending of the substrate can lead to package damage and should be avoided in the assembly flow. Avoid Excessive Bending Figure 3-6. Avoid Excessive Bending SLUA271C 窶� JUNE 2002 窶� REVISED DECEMBER 2023 Submit Document Feedback Copyright ツゥ 2023 Texas Instruments Incorporated QFN and SON PCB Attachment 9 Solder Paste Screen Printing Process www.ti.com 4 Solder Paste Screen Printing Process 4.1 Solder Paste The quality of the paste print is an important factor in producing high-yield assemblies. The paste is the vehicle that provides the flux and solder alloy necessary for a reliable and repeatable assembly process. A low residue, no-clean solder (SN63/Pb37 or SAC alloy) paste is commonly used in mounting QFN and SON, however, watersoluble flux materials can be used as well if the residues can be adequately cleaned from the board. Typically, the choice of solder paste determines the profile and reflow parameters. Most paste manufacturers provide a suggested thermal profile for their products and must be referenced before manufacturing. Special SMD-specific solder pastes are being marketed by paste vendors that minimize voiding in the solder joint. If low-standoff parts such as CSPs and QFNs are to be used, highly aggressive solder fluxes are not recommended unless they can be cleaned from under the parts. TI recommends that the solder-paste manufacturer窶冱 recommended temperature profile be used to optimize flux activity within the MSL (moisture sensitivity level) guidelines for the most thermally sensitive component. Refer to J-STD-033 for more details on MSL classification. 4.2 Solder Stencils The formation of consistent solder joints is a necessity. The contrast between a large exposed pad and small lead fingers of the QFN and SON can present a challenge in producing an even standoff height. To this end, careful consideration must be applied to the stencil design. The stencil thickness, as well as the stencil opening geometry, determines the precise volume of solder paste deposited onto the device land pattern. Stencil alignment accuracy and consistent solder volume transfer are critical for uniform reflow solder processing. Stencils are usually made of nickel buildup or stainless steel, with a nickel buildup stencil offering a smoother side wall over a laser-cut stainless steel stencil. Apertures are typically trapezoidal, which helps to ensure uniform release of the solder paste and reduce smearing (see Figure 4-1). The solder-joint thickness of QFN and SON lead fingers is typically between 0,050 mm to 0,075 mm, which has a direct relationship to the amount of solder printed on the center thermal pad area. Thickness of stencils used in manufacturing varies from 0,100 mm to 0,150 mm (0.004 in to 0.006 in) range, with a typical 0,125 mm stencil design for 0,5 mm pitch components. The actual thickness of a stencil is dependent on other surface-mount devices on the PCB, in addition to the area and aspect ratio of the minimum aperture used. Use a squeegee with a durometer of 95 or harder, such as stainless steel. The blade angle and speed must be fine tuned to ensure an even paste transfer. An inspection of the printed solder paste is recommended before placing parts. A repeatable solder deposit is the most important factor for robust reflow yields further downstream in the process. As a guide, a stencil thickness of 0,125 mm (0.005 in) for QFN and SON components is recommended. IPC-7525 outlines the necessary parameters to consider when designing the stencil. Side View Stencil A B C PCB Stencil Apertures Should be Tapered to Figure 4-1. Solder Stencil Profile 4.3 Lead Finger Stencil Design The stencil aperture is typically designed to match the PCB or substrate pad size 1:1 (1:1 is recommended on periphery lead fingers and not the center thermal pad 窶� see Section 4.4 for exposed pad recommendations). For fine-pitch QFN and SON components of 0,5 mm and below, it can be necessary to reduce the stencil 10 QFN and SON PCB Attachment SLUA271C 窶� JUNE 2002 窶� REVISED DECEMBER 2023 Submit Document Feedback Copyright ツゥ 2023 Texas Instruments Incorporated www.ti.com Solder Paste Screen Printing Process aperture by 20% to prevent shorting beneath the QFN, paying special attention that the area or aspect ratios are not exceeded. This reduction is recommended in cases where the SMT equipment placement force is not well regulated, leading to shorting from excessive solder-paste squeeze out. For 0,4-mm pitch components, a pad width of 0,2 mm is recommended to aid solder-paste printing and to achieve a gap of 0,2 mm between pads. Lead finger stencil dimensions depend on the specific QFN and SON lead finger dimensions. For example, on a 0,5-mm pitch device with 0,85-mm x 0,28-mm wide pads, a stencil aperture of 0,23 mm x 0,8 mm and thickness of 0,125 mm should be used to achieve adequate print volume and area ratio requirements as outlined in IPC-7525 (see Figure 4-2). In cases where the board land pattern must be minimized, the stencil aspect and area ratios should be considered before board design. The area ratio of the stencil is critical for the printing to get good paste release. For very small apertures where the area ratio is less than 0.66, the stencil must be nickel formed. This type of stencil has superior release characteristics over stencils that have been produced by laser. Experiments have shown that nickelformed stencils print with area ratios down to 0.57. Check with your stencil supplier for recommendations when designing an aperture with a challenging area ratio. The aspect ratio relates to the manufacture of stencils. Stencil manufacturers require the aspect ratios (see Figure 4-2) to be greater than 1.5 (see IPC-7525). The higher the area ratio, the better the solder paste releases, in addition to depositing more volume. Stencil thickness is inversely proportional to the area ratio. So the thinner the stencil, the higher the area ratio will be, ultimately resulting in a robust solder-paste release (see IPC-7525). L W Width of Aperture Opening Aspect Ratio = = Stencil Foil Thickness T Area of Aperture Opening W Area Ratio = Area of Aperture Walls WxL = 2 x (L + W) x T T Figure 4-2. Aspect and Area Ratio Illustration 4.4 Exposed-Pad Stencil Design The QFN and SON package is thermally and electrically efficient due to the exposed die attach pad on the under side of the package. The exposed die must be soldered to the PCB or motherboard substrate. It is good practice to minimize the presence of voids within the exposed pad interconnection. Total elimination is difficult, but the design of the exposed pad stencil is crucial. The proposed stencil design enables out-gassing of the solder paste during reflow and also regulates the finished solder thickness. Typically, the solder-paste coverage is approximately 50% to 70% of the pad area (see Figure 4-3). Designing an aperture that prints solder 1:1 with the exposed pad results in excessive metal volume that can "float" the part and cause opens and other manufacturing defects. In addition, the amount of voiding post reflow in the thermal pad solder joint should not exceed 50% in high-power applications (to be verified using an x-ray). Based on a JEDEC High K board stackup, 25% has been determined to be a point of diminishing thermal performance returns, but TI prefers a limit of 50% to be set (reference JESD51-7). SLUA271C 窶� JUNE 2002 窶� REVISED DECEMBER 2023 Submit Document Feedback Copyright ツゥ 2023 Texas Instruments Incorporated QFN and SON PCB Attachment 11 Solder Paste Screen Printing Process www.ti.com Figure 4-3. Example Land Pattern and Exposed-Pad Stencil Design 12 QFN and SON PCB Attachment SLUA271C 窶� JUNE 2002 窶� REVISED DECEMBER 2023 Submit Document Feedback Copyright ツゥ 2023 Texas Instruments Incorporated www.ti.com Package to Board Assembly Process 5 Package to Board Assembly Process 5.1 Placement and Alignment The pick and place accuracy governs the package placement and rotational (theta) alignment. This accuracy is equipment and process dependent. Slightly misaligned parts (less than 50% off the pad center) automatically self align during reflow (see Figure 5-1). Grossly misaligned packages (greater than 50% off pad center) must be removed before reflow, as they can develop electrical shorts resulting from solder bridges if they are subjected to reflow. There are two popular methods for package alignment using machine vision: 窶「 Package silhouette, also called "back lighting". The vision system locates the package outline. 窶「 Lead-frame recognition, also called "front lighting". Some vision systems can directly locate the lead-frame pattern. Both methods are acceptable for QFN and SON placement. The front lighting recognition type alignment tends to be more accurate, but is also slower because more complex vision processing is required on the pick and place machine. The package silhouette method allows the pick and place system to run faster, but it is generally less accurate. Both methods are acceptable and have been successfully demonstrated by major pick and place equipment vendors and contract assembly houses. A starting placement force of 1.5N is recommended and should be minimized where possible. After a placement force is selected, inspect all four sides of the QFN package to make sure that each side is seated in the solder paste. Excessive pressure can cause shorting due to solder squeeze out from under the part and, in extreme cases, can potentially crack the package. Location of the thinner QFN packages should be carefully considered. Excessive bending of the substrate can also lead to package damage and should be avoided in the assembly flow. 5.2 Solder Reflow There are no special requirements necessary when reflowing QFN and SON components. As with all SMT components, it is important that profiles be checked on all new board designs. In addition, if there are multiple packages on the board, the profile must be checked at different locations on the board. Component temperatures can vary because of surrounding components, location of the device on the board, and package densities. To maximize the self-alignment effect of QFN and SON, it is recommended that the maximum reflow temperature specified for the solder paste not be exceeded. A good guide is to subject the PCB to a temperature ramp not exceeding 4ツーC per second. The reflow profile guidelines (see Figure 5-2) are based on the temperature at the actual solder-pad to PCB land-pad solder joint location. The actual temperature at the solder joint is often different than the temperature settings in the reflow/rework system, due to the location of the system thermocouple used to monitor the temperature. Specific production reflow and rework systems vary depending on manufacturer and model. Therefore, system specific profiles must be established using thermocouples at the actual solder joint locations. TI has tested and qualified QFNs and SONs for three reflow operations according to JEDEC J-STD-020. This allows one reflow operation per side of the PCB (assuming the use of a double-sided PCB) and one rework operation if necessary. TI recommends use of the temperature profile from the solder-paste manufacturer to optimize flux activity within the MSL guidelines for the most thermally sensitive component. See J-STD-033 for more details on MSL classification. SLUA271C 窶� JUNE 2002 窶� REVISED DECEMBER 2023 Submit Document Feedback Copyright ツゥ 2023 Texas Instruments Incorporated QFN and SON PCB Attachment 13 Package to Board Assembly Process www.ti.com Before Reflow During Reflow After Reflow Figure 5-1. Package Self Alignment at Reflow Temperature (ツコC) SnPb Temperature Profile Example Max. 235ツーC, Min. 195ツーC 183 165 135 Min. 60 sec. Max. 120 sec. Min. 30 sec. Max. 90 sec. Time Temperature (ツコC) Pb-Free Temperature Profile Example Max. 260ツーC, Min. 230ツーC 220 180 150 Min 30 sec. Min. 60 sec. Max. 120 sec. Max. 90 sec. Time Figure 5-2. QFN and SON Pb and Pb-Free Example Reflow Profiles 5.3 PCB Cleaning If a low-residue no-clean solder paste is used, PCB cleaning typically is not required. With the elimination of materials containing chlorofluorocarbon (CFC), most companies have moved to either a no-clean or aqueous flux-based system. No-clean fluxes and solders minimize the harmful effects that residues left on the board can cause in the form of corrosion. Because a wide variety of no-clean solder pastes are available, perform application-specific evaluations to identify if any remaining residues can cause harm to the assembly. Contact your solder-paste supplier for testing performed and recommended-use conditions. Evaluate the cleaning process for water-soluble fluxes and give special attention to cleaning under the QFN component. Due to the wide variety of cleaning mediums on the market outside of TI窶冱 control, each customer should discuss material interactions with their supplier before cleaning. In addition to cleaning, the drying of circuit boards of any residual cleaning medium must be considered to prevent potential issues such as corrosion. 5.4 Inspection Inspection of QFNs and SONs on a PCB typically is accomplished by using transmission type x-ray equipment. In most cases, 100-percent inspection is not performed. Typically, x-ray inspection is used to establish process parameters and then to monitor the production equipment and process. Transmission x-ray can detect bridging, shorts, opens, and solder voids. There are many different types of x-ray inspection equipment available and 14 QFN and SON PCB Attachment SLUA271C 窶� JUNE 2002 窶� REVISED DECEMBER 2023 Submit Document Feedback Copyright ツゥ 2023 Texas Instruments Incorporated www.ti.com Package to Board Assembly Process functionality varies. X-ray inspection system features range from manual to automated optical inspection (AOI). Different systems also provide single-dimensional or multidimensional inspection capabilities. As explained in Section 5.2, QFNs and SONs self align to the land pad using surface tension during the solder reflow process. As a result, it is unlikely that a QFN and SON is marginally misaligned. If a misalignment does occur, it is likely to be by an entire pad. This effect makes it possible to do a gross visual alignment check after the reflow. Fiducial marks on the PCB can aid visual checks of the PCB and also are useful for manually placing units during any rework. The exterior fillet formation can vary based on manufacturing factors, such as flux activity, solder volumes, and overall standoff height. Due to factors outside of TI窶冱 control, no assurance for consistent solder fillet heights on the package sides during assembly can be made. IPC-A610D does not require a side fillet, since the side terminations are not plated. While it can appear the wetting is reduced on the side of the component, the solder joint underneath is not affected (see Figure 5-3). Figure 5-3. Illustration of Typical Fillet Formation SLUA271C 窶� JUNE 2002 窶� REVISED DECEMBER 2023 Submit Document Feedback Copyright ツゥ 2023 Texas Instruments Incorporated QFN and SON PCB Attachment 15 Rework Guidelines (Hot Gas Convection and Manual) www.ti.com 6 Rework Guidelines (Hot Gas Convection and Manual) Rework equipment has continued to progress rapidly to address chip scale packages. Many manufacturers use a single rework station to incorporate multiple rework process steps, such as component removal, site redress, solder paste and flux application, alignment, component placement, and reflow. The advancement of beam-splitting imaging for alignment, placement, and other areas, such as characterizing and storing individual component reflow profiles, has greatly simplified the rework process. Because QFNs and SONs allow more functionality and features on smaller products, one area of concern is thermal separation of adjoining components during the rework process. Some manufacturers have addressed this concern by designing hot gas nozzles that maintain the keep-out zone area around the rework component to thermally isolate adjacent components during the reflow process. Original equipment manufacturers have different requirements for solder-paste and flux-only applications during the rework process. For those who require solder paste, microstencils and squeegees have been developed. These microstencils are aligned using the same beam-splitting imaging as the component placement. Microsqueegees allow for simple, uniform solder-paste coverage across the microstencil. Section 6.3 shows the technique of screen-printing solder to the component before placement. 6.1 Compound Removal It is highly recommended to bake out the board before rework to reduce the risk of delaminating either the board or part. Removing the component is by far the easiest part of the rework process. After the thermal profile is optimized, the process parameters are used to remove the device. The gas nozzle used during this process surrounds the device and seals against the board. The QFN or SON is heated from the top side with hot gas, while residual heat is exhausted up and away from adjacent components. The anti-crushing feature in the nozzle prevents excessive top-side force from being applied to the QFN and SON. The entire assembly is also heated from the bottom side with an under-board heater to help prevent warpage. Preheating the board to a fixed temperature before the component is heated also helps to ensure process repeatability. When the reflow process is complete, the nozzle vacuum cup is automatically activated and the component is slowly lifted off the pads. The vacuum cup in the nozzle is designed to disengage if the component has not fully reflowed for any reason. This prevents the potential for lifting pads. The application of flux is recommended for QFN and SON removal. Table 6-1 lists generic guidelines to remove QFN packages assembled on a 0.056-in FR4 board. It is recommended to modify heating profiles for different board thicknesses and equipment used. Parts must not exceed the peak temperature as listed on the MSL label. Parts and boards must be baked out before rework to reduce the risk of delamination. Table 6-1. Pb-Free Solder Component Removal 1. Apply flux paste to component. 2. Align nozzle over part to be removed. 3. Maintain nozzle 0.050-in over device. Take care to prevent overtravel of the vacuum tip, which can damage the part or vacuum tip when measuring this distance. 4. Preheat board to 90ツーC, nozzle warming up 20% air flow, 125ツーC 5. Soak stage: 20% air flow, 225ツーC, 90 s 6. Ramp stage: 20% air flow, 335ツーC, 30 s 7. Reflow stage: 25% air flow, 370ツーC, 65 s 8. Enable vacuum at the end of the reflow cycle, lower vacuum nozzle, and remove part. 9. Cool down stage: 40% air flow, 25ツーC, 50 s 10. Turn off the vacuum and remove part from nozzle. 11. Using any metal tweezers or rough handling can damage the part and render it unanalyzable. 12. Do not reuse the part after it is removed. 16 QFN and SON PCB Attachment SLUA271C 窶� JUNE 2002 窶� REVISED DECEMBER 2023 Submit Document Feedback Copyright ツゥ 2023 Texas Instruments Incorporated www.ti.com Rework Guidelines (Hot Gas Convection and Manual) 6.2 Site Redress After the QFN and SON has been removed, the residual solder that remains on the board pads must be removed. The QFN or SON PCB site is very fragile due to its extremely small pad sizes. To avoid damaging the pads or solder mask, the site redress process must be performed very carefully. Apply flux to the site after component removal. Use a temperature-controlled soldering iron fitted with a small flat blade to gently apply solder braid that has been presoaked in flux over the PCB pads. Remove residual flux from the site with alcohol and a lint-free swab. Then inspect the site before the replacement process. Do not use the removed part. The added volume of solder on the removed part causes coplanarity issues and inconsistent solder volume. Performing site redress on the periphery leads of the component can also cause unforeseen damage. 6.3 Component Replacement and Reflow The first step before replacement is to apply solder paste either to the board or directly to the component. Depending on the application, one of these two methods can be more advantageous, due to factors such as board density and ease of access to the rework site. Evaluate which method is best on a case-by-case basis. Both methods require the use of a mini stencil. Figure 6-1 shows the steps to screen print solder directly onto the component. The solder paste is applied to the part using a fixture courtesy of Photo Stencil. A component insertion tool ensures proper registration of lightweight QFNs and SONs onto the printed circuit board. In addition, the insertion tool eliminates manual handling of the component, which can deposit unwanted skin oil on the component pads. Optical systems used for alignment consist of a beam-splitting prism combined with an inspection microscope or video camera fitted with a zoom lens. This optical system allows the operator to see a magnified image of the bottom side of the QFN and SON superimposed over the corresponding PCB land pattern. Alignment and placement of the QFN and SON must be accurate to within 0,1 mm. When the QFN and SON is correctly aligned, the X-Y table is locked to prevent further movement. The nozzle (Figure 6-2) is lowered until it lightly contacts the board. The nozzle vacuum is automatically deactivated and the thermal reflow cycle begins. PC-based software provides the process control necessary to ensure repeatable results. Once the cool-down stage is complete, the nozzle is raised and the assembly is removed for inspection. Figure 6-1 shows generic guidelines to remove QFN packages assembled on a 0.056-in FR4 board. It is recommended to modify heating profiles for different board thicknesses and equipment used. Parts must not exceed the peak temperature as listed on the MSL label. Parts and boards must be baked out before rework to reduce the risk of delamination. SLUA271C 窶� JUNE 2002 窶� REVISED DECEMBER 2023 Submit Document Feedback Copyright ツゥ 2023 Texas Instruments Incorporated QFN and SON PCB Attachment 17 Rework Guidelines (Hot Gas Convection and Manual) www.ti.com Figure 6-1. Example Mini Stencil Example Air-Vac Rework Nozzle for QFN Package sizes between 2.15 mm to 4.5 mm ト� NMX188DVG - .188窶� Exhaust Opening - Used for QFN Package sizes between 2.15 mm to 4.5 mm - VTMX020-35 Vacuum Tip ト� A larger nozzle will be required for larger package sizes. ト� Refer to www.air-vac-eng.com for recommended nozzle sizes by package dimension Hot Gas Convection Nozzle Figure 6-2. Example Hot Gas Convection Nozzle 18 QFN and SON PCB Attachment SLUA271C 窶� JUNE 2002 窶� REVISED DECEMBER 2023 Submit Document Feedback Copyright ツゥ 2023 Texas Instruments Incorporated www.ti.com Rework Guidelines (Hot Gas Convection and Manual) Table 6-2. Pb-Free Solder Component Placement 1. Apply solder paste to component or board using mini-screen printing tool (see Figure 6-4). 2. Align device over pads. 3. Place device on board. Take care to prevent overtravel during placement, which can damage the part or vacuum tip. 4. Raise nozzle 0.050-in 5. Preheat board to 90ツーC, nozzle warming up 20% air flow, 125ツーC. 6. Soak stage: 20% air flow, 225ツーC, 90 s 7. Ramp stage: 20% air flow, 335ツーC, 30 s 8. Reflow stage: 25% air flow, 370ツーC, 65 s 9. Cool down stage: 40% air flow, 25ツーC, 50 s 6.4 Manual Rework Considerations If manual touch-up is required, it is highly recommended to bake out the board and replacement components before rework, which reduces the risk of delaminating either the board or part. Use of a preheater (see Figure 6-3) is also strongly recommended to reduce the risk of temperature overshoot. By using a preheater, the soldering iron tip size and potential for temperature overshoot can be reduced, resulting in a robust manual soldering iron process. IPC7711 recommends initial use of the lowest possible tip temperature. It is also recommended that the smallest tip size be used, which mitigates temperature overshoot and reduces the risk of delaminating either the board or component. Damage can result when a soldering iron comes in contact with the periphery lead, and pressure is applied to the side of the QFN part. Avoid contacting the side of the QFN part when performing manual rework with a soldering iron or damage will occur (see Figure 6-4). If manual soldering is used, the soldering iron tip should only contact the board pad without contacting the side of the component. In general a temperature-controlled hot gas convection repair method is recommended over manual soldering because the risk of applying excessive force is eliminated. The maximum rework temperature as measured on the package should not exceed the MSL rating as specified on the shipping label. See Figure 2-1 for an example of the MSL label. Figure 6-3. Preheater SLUA271C 窶� JUNE 2002 窶� REVISED DECEMBER 2023 Submit Document Feedback Copyright ツゥ 2023 Texas Instruments Incorporated QFN and SON PCB Attachment 19 Revision History www.ti.com Figure 6-4. Manual Rework Damage 7 Revision History Changes from Revision B (August 2018) to Revision C (December 2023) Page 窶「 Updated the numbering format for tables, figures, and cross-references throughout the document................. 1 Changes from July 25, 2007 to August 28, 2018 Page 窶「 Editorial and format changes throughout document...........................................................................................1 20 QFN and SON PCB Attachment SLUA271C 窶� JUNE 2002 窶� REVISED DECEMBER 2023 Submit Document Feedback Copyright ツゥ 2023 Texas Instruments Incorporated IMPORTANT NOTICE AND DISCLAIMER TI PROVIDES TECHNICAL AND RELIABILITY DATA (INCLUDING DATA SHEETS), DESIGN RESOURCES (INCLUDING REFERENCE DESIGNS), APPLICATION OR OTHER DESIGN ADVICE, WEB TOOLS, SAFETY INFORMATION, AND OTHER RESOURCES 窶廣S IS窶� AND WITH ALL FAULTS, AND DISCLAIMS ALL WARRANTIES, EXPRESS AND IMPLIED, INCLUDING WITHOUT LIMITATION ANY IMPLIED WARRANTIES OF MERCHANTABILITY, FITNESS FOR A PARTICULAR PURPOSE OR NON-INFRINGEMENT OF THIRD PARTY INTELLECTUAL PROPERTY RIGHTS. These resources are intended for skilled developers designing with TI products. You are solely responsible for (1) selecting the appropriate TI products for your application, (2) designing, validating and testing your application, and (3) ensuring your application meets applicable standards, and any other safety, security, regulatory or other requirements. These resources are subject to change without notice. TI grants you permission to use these resources only for development of an application that uses the TI products described in the resource. Other reproduction and display of these resources is prohibited. No license is granted to any other TI intellectual property right or to any third party intellectual property right. TI disclaims responsibility for, and you will fully indemnify TI and its representatives against, any claims, damages, costs, losses, and liabilities arising out of your use of these resources. TI窶冱 products are provided subject to TI窶冱 Terms of Sale or other applicable terms available either on ti.com or provided in conjunction with such TI products. TI窶冱 provision of these resources does not expand or otherwise alter TI窶冱 applicable warranties or warranty disclaimers for TI products. TI objects to and rejects any additional or different terms you may have proposed. IMPORTANT NOTICE Mailing Address: Texas Instruments, Post Office Box 655303, Dallas, Texas 75265 Copyright ツゥ 2023, Texas Instruments Incorporated